Aluminum Die Casting / Casting Preventive Maintenance and Defective Rates Reduction
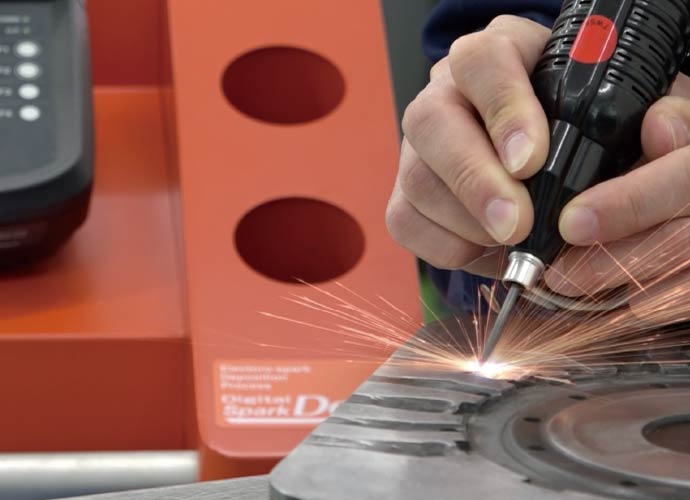
Dies Corrosion, Erosion, and Heat Crack Prevention
Product Defective Rates Reduction
Common issues of Diecasting and Casting dies are corroded and eroded by high speed molten Aluminum etc. on dies surface.
And heat cracks are occurred due to expansion by heating and shrinkage by cooling.
Depo series dramatically solve these issues to execute Coating by cermet electrodes to prevent Erosion, Seizing, Scuffing, and Heat-Cracking.
And Maintain Liquid Flow to prevent Underfill to reduce production defective rates.
Erosion Test of Coating in Molten Aluminum
Weight Loss of Coating Sample was less than 1/10 comparing to Non-Coating Sample.
Test Condition / Sample: SKD-61, Molten Al: ADC12 (680℃) rotated at 30rpm
-
Erosion Resistance Test 1
*Tungsten-Carbide -
Erosion Resistance Test 2
Erosion Mount: 1/10 or less comparing to Non-Coating
Coating Effectiveness
Wearing Prevention
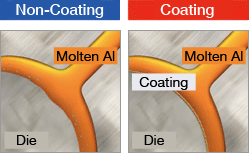
Non-Coating | Molten Al flows rapidly into die. Then, fraction is occurred and Wearing is in progress on surface of die. |
---|---|
Coating | Against hardness 350-400HMV die, Coating layer by cermet electrode that is hardness more than 2000HMV extremely protects die surface. |
Erosion Prevention
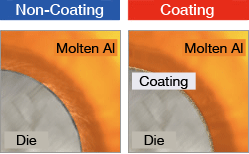
Non-Coating | Die surface is occurred erosion contacting with high temperature molten Al. |
---|---|
Coating | Preventing erosion amount within 1/10 from die surface by worse wettability coating material. |
Seizing & Scuffing Prevention
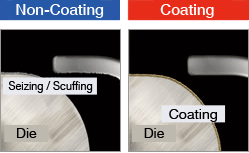
Non-Coating | Molten Al and die surface are easy to react each other, seizing and scuffing are occurred at contact area. |
---|---|
Coating | Preventing seizing and scuffing by uneasy-react (worse wettability) coating material against molten Al. |
Heat Cracks Prevention
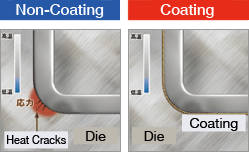
Non-Coating | Stress is accumulated in die surface with repetition of Heat by teeming molten Al (Expanding) and Cooling by die lubricant (Shrinkage) occurring Heat Cracks. |
---|---|
Coating | Insulation effects of Intercalated minute air in slight roughness die surface (tongued and grooved face) by coating controls expanding and shrinking to prevent Heat Cracks occurred. |
Maintain Liquid Flow and Underfill Prevention
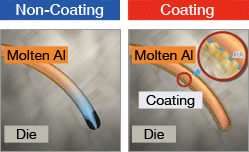
Non-Coating | Underfill is occurred in product when molten Al contacts cooled die surface and cooling down to reduce liquid flow. |
---|---|
Coating | Insulation effects of Intercalated minute air in slight roughness die surface (tongued and grooved face) by coating keeps liquid temperature and flow to prevent Underfill occurred. |
Control Flow Direction and Liquid Flow Line Prevention
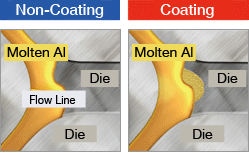
Non-Coating | Liquid flows along die design and is occurred Flow Line at cold shut. |
---|---|
Coating | Coating with certain degree of surface roughness at cold shut controls flow directions uniformly to prevent Flow Line by its turbulence. |
Related Product
Coating and Overlay Device
Depo Series〈Depo〉
Best Solution for Preventive Maintenance and Over Repairing of Machine Parts, Mold and Dies
Depo Series are a newer Coating and Overlay method applying EDM (Electrical Discharge Machining) principle.
Depo Series are a newer Coating and Overlay method applying EDM (Electrical Discharge Machining) principle.